EASI Webinar - Part 1
Title: EASI Webinar 1
Date: Tuesday, March 15, 2011
Time: 11:00 AM - 12:00 PM PDT
The EASI Standards Group will be conducting a one hour online informational Webinar. Attendees of the Webinar will get an easy to follow crash course in EDI and the EASI Standards. The session is available for interested, new, and current users of the standards.
Topics will include:
-
A basic explanation of EDI
-
A brief history of the EASI Group
-
An explanation of our most fundamental standards
-
Use of GTIN numbers
-
Carton Label Standards
-
EDI Routing Envelopes
-
832 Product Descriptor Databases (PDD’s)
-
850 Purchase Orders
-
856 Advanced Shipment Notifications (ASN’s)
Learn about the EASI Standards and what they can do for you and your company.
Webinar 1
A Basic Explanation of EDI
The acronym EDI stands for Electronic Data Interchange. It is the communication of information from one computer system to another. Basically, EDI represents the communication of the same forms you exchange on a daily basis with your customers and vendors, but in digital form. Instead of a Purchase Order form that is faxed to your trading partner and entered manually into their system, your computer system transmit a specially formatted electronic file containing the same information. This electronic form can be "pulled in" (read) by the receiving computer system. Using EDI, manual entry of the faxed PO is not necessary.
This process vastly reduces the time it takes to get that PO into your trading partner's system. At the same time it removes the possibility of manual entry errors. You get the correct product faster.
This same process can be automated for other forms; Advanced Shipment Notifications (packing slips), Invoices, Point of Sale data, Item information, etc.
The EASI Standards group has created a Standard for each of these Forms. The purpose of having a Standard is to remove the need to customize the structure and content for each trading partner and form. If you have 10 trading partners and each had a unique structure for a Purchase Order form, your computer system would need to handle all 10 versions. With the EASI Standards you are able to define the structure once, and connect with all your customers who comply with that single Standard.
An important note about EDI files: They are not intended to be human readable. If you were to view an EDI file it may appear to you to be gibberish. The good news is, if your computer system has been configured to comply with the standard, your computer knows how to interpret the "gibberish" and translate it appropriately. You can also use the Standard layout file (available on this site) to translate an EDI file visually, but, to be frank, it's no fun, leave it to your computer.
So when people mention EDI it is often simplest to think about a form you would normally fax, email, or mail, and consider the EDI version as simply a digitial verson of that same form. That digital version is communicated from your system directly to your trading partner's system.
We'll touch on some more detailed information about the structure of an EDI file at the end of the webinar if there is time and if anyone is interested.
In addition to the Documentation section of the website, the group has put together a downloadable pdf, the EASI 101 Guide, which you can download here. For additional information about the basics of EDI and it's use please visit our EDI Resources Page.
A brief history of the EASI Group
In the late 90's a group of activewear mills and distributors got together to discuss the challenges facing the industry. They identified the lack of standards and practices as a key area for improvement. The difficulties in dealing with customized information exchange between every partner consumed resources, increased errors, and negatively impacted the supply chain. Standardizing communication methods, EDI layouts, carton labels, and establishing a common item reference (GTIN) and barcode promised multiple benefits.
-
Data Entry Time and Cost
-
Reduction in Errors and Discrepancies
-
Reduction in Labor Costs
-
Reduction in IT programming/customization
-
Improved communication and access to critical information
With these goals in mind the EASI Standards Group was launched. The group was tasked with establishing standards and practices related to the exchange of supply-chain related information. Today those standards can realize benefits in every department; Accounting, Purchasing, Customer Service, Distribution, Marketing, IT.
The non-profit group meets annually to discuss ongoing compliance opportunities, improve the standards, discuss new ways of increasing efficiencies while reducing costs, and vote on new Standards or new versions of existing standards.
A few years ago, the membership structure was changed from annual membership fees to a one time contribution. The group is lead by an elected Steering Committee which oversees the administration of the group and the activities of the Technical Committee. The group is also made up of Full Members (who have voting rights) and Interested Parties (who do not have voting rights) as well as several key Apparel Industry Software Providers.
For a more detailed history see our History Page. Click here to find out How to Become and EASI Member or here to see a list of the Current Members. You may also find answers to your EASI questions by visiting our FAQ page.
An explanation of our most fundamental standards
Every company in our industry handles a specific set of key forms and deals with inventory labels. There are very few exceptions. The EASI Group focused on these key forms and labels. Purchase Orders, Advanced Shipment Notifications (aka "ASN's" or "packing lists"), Invoices, and Master Carton Labels. With this primary set of EDI documents a compliant partner can go a long way to reducing manual entry time, mistakes and the financial impact of both.
While full compliance with all the standards is strongly encouraged, companies who use the standards can pick and choose which standards they want to comply with. One reason full compliance is encouraged is based on the integrity of the data. If a company wishes to received EDI ASN's from their mill to improve receiving time and supply chain visibility, it would be difficult for the mill to maintain accurate data without the Purchase Order being issued via EDI transmission. The ASN depends on data found in the PO. Leave it up to manual entry and you're dealing with a broken chain.
The EASI Group also supplies a standard for the size, layout and content on carton labels. By standardizing carton labels Distribution Centers can more easily move those cartons through their systems. And by ensuring each carton contains a standard barcode with a known value paperless and RF-based warehouse systems can scan each carton. No more of this:
In the above example, telling a computer system what barcode value from a mill equals what SKU number in a distributor's inventory system adds an incredible amount of expense, in addition to the ease in which warehouse personnel can identify the product based on a myriad of layout and content possibilities. With the EASI Carton Label trading partners deal with a single layout, standard content, and a standard barcode.
But before companies can start trading these key forms electronically and using the standard carton labels, some fundamental processes and systems need to be in place.
Use of GTIN numbers
Prior to the EASI Standards there was no agreement on which identification number trading partners should use. For Product A the Distributor uses SKU Number YYY. The Mill uses SKU number ZZZ for that same product. A Distributor places an order using their SKU number YYY, the Mill communicates the shipment of that product using their SKU number ZZZ. The carton label received at the Distributor's warehouse says ZZZ. How can the receiving warehouse identify the product? If they look on the packing slip they'll see the Mill's SKU number ZZZ.
And this was the case for every trading partner and for every SKU processed through the supply chain.
Enter the GTIN - a Global Trade Identification Number. One item number to rule them all.
By adopting the use of GTIN numbers for item identification, the Mill and all Distributors can use a single item number for Product A. The Mill's system now says for Product A my GTIN is WWW. The distributor now says product A's GTIN number is WWW. The Distributor places an order for WWW, the Mill sends a shipment notification that WWW has shipped. The carton arrives in the Distributor's warehouse with a barcode that says WWW. The barcode is scanned and reads WWW, and the distributor's system knows that Product A has been received.
GTINs are very similar to UPC codes in the retail industry. Instead of a 12 digit UPC the EASI group adopted the 14 digit GTIN. The GTIN number is made up of "Indicators", a unique company prefix (assigned by the GS1 organization - the same organization which controls upc codes) along with an incremental serial number, and lastly a "check digit" used for verification purposes.
So a GTIN which may look randomn: 00846503003946
Actually has some intelligence built in:
00 8465030 0394 6
-
00 = Application Identifier ("I'm a item")
-
8465030 = Company Prefix ("Company ABC made me")
-
0394 = Item ID ("I'm item number 0397")
-
6 = Check Digit ("I'm here for your barcode scanners to make sure they can read the barcode correctly.")
With this data combination I am a globally unique item number. No one else can use this item number and no one should mistake it for a different product.
This may be overload for some, but the point is, just like EDI files in general, humans shouldn't really look at GTIN numbers. Let your computer systems and barcode scanners do the work for you.
Click on the following links for more information about the GS1 organization and EASI's use of GTIN numbers.
Carton Label Standards
As mentioned above, the EASI Group has standardized the layout, content, and placement of labels on Cartons moving through the supply chain - from the Mill to the Distributor.
The arrows point to unique elements of data that are present on each carton label.
While there are some complex elements (like the generation of the SSCC-18 - a unique carton license plate) most of the information is farily straight forward. There is a field that displays which company manufactured the product, descriptive fields about what the product is, and barcodes which can be read by scanners when "transacting" the carton through various stages (Receipt, Shipment, Cycle Counting, Stock Adjusting, etc.).
The standard also dictates where these labels should be placed on cartons in order for automated scanning systems to make full use of the barcodes and maximize the efficiency of certain processes. Distribution Centers no longer need to hunt for a carton label (placed on the top of a carton that's in the middle of a stack), they no longer have to interpret the data based on different companies inclusion/exclusion of data, and they can scan each carton instead of manually key in an item number which their system may or may not know.
Visit the EASI Master Carton Label Standard page to learn more about their content and use.
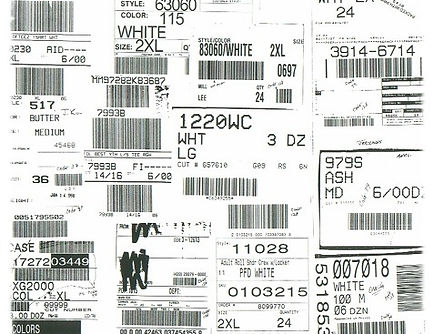
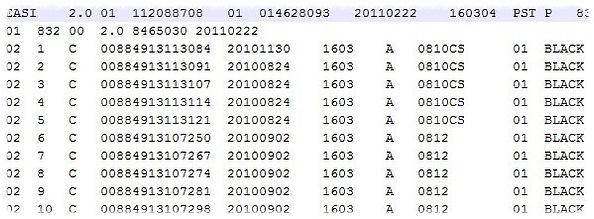
